As ever-evolving corrugating technologies demand increased efficiencies, corrugators turn to banding to improve bundling and streamline their processes. While many companies already reap the benefits of banding, some are hesitant to stray away from strapping. Why? Because of a few myths…
1. TOO DIFFERENT
For decades, strapping was the only bundling solution used by corrugators nationally (and globally). When introduced to banding, most are hesitant to consider a new technology because a new solution is difficult to learn. Right? Not always.
While banding is certainly different than strapping in more ways than one (see points 2, 3, and 4), the additional time and space required to adapt to the technology is minimal. Most banding machines, especially off-line machines, look nearly identical and operate in a fundamentally similar way to those used for strapping.
2. TOO NEW
Similar to 1, hesitancy to consider banding often results from a concern that the technology is too new to the corrugated industry. What most don’t know, though, is that banding has been a strong alternative to strapping for over two decades and has replaced strapping entirely in hundreds of production facilities.
3. TOO WEAK
Unlike strapping which typically uses a heat-weld sealing system, high-end banding machines operate with tension-adjustable ultrasonic technology. This allows for custom welds to be created for nearly any application; material can be welded just strong enough to pull apart or strong enough to require a tool for removal.
In addition, banding material can create a strong bundle but is gentle enough not to ruin the top and bottom layers of each bundle. PLUS, without heat, the welded banding material will not adhere to your corrugated material and tear products upon removal.
4. TOO EXPENSIVE
The most widely believed myth about banding is that the technology is too expensive. However, the most widely overlooked statistics (and prices) are those related to post-purchase productivity. Not only does introducing banding automation to a production line reduce labor costs, it decreases material waste from a master carton, helps increase productivity and, ultimately, quickly generates ROI.
But, what about material? While the up-front cost may be a bit more than strapping material, the gentle yet strong hold of the material will not ruin bundles, therefore reducing wasted product.
Interested in learning more about strapping alternatives? Contact us anytime – we’d love to introduce you ultrasonic banding!
MORE INSIGHT...
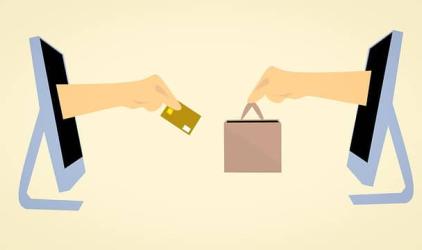
LOOK OUT FOR THESE E-COMMERCE PACKAGING TRENDS IN 2024
Discover the upcoming packaging and e-commerce trends in 2024. These changes are set to reshape the way products are packaged and delivered, focusing on sustainability, efficiency, and creative solutions. Let’s take a closer look at the…
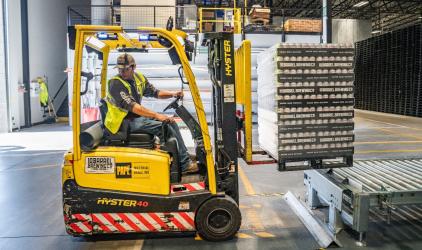
Pain Point Solutions for Manufacturing Business Growth
In the ever-evolving business landscape, every company faces unique challenges and pain points that require careful adaptation and innovative solutions. Whether it’s dealing with worker injury, labor shortages, or increasing customer demands, the…
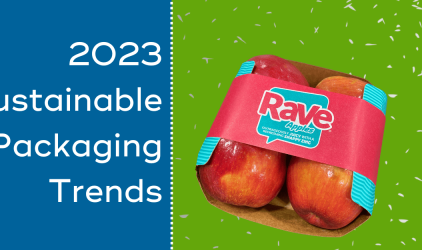
SUSTAINABLE PACKAGING TRENDS TO LOOK FOR IN 2023
INTRODUCTION Sustainable packaging is becoming increasingly important as consumers demand more environmentally-friendly products. In 2023, we can expect to see a variety of new sustainable packaging trends emerge. This blog post will explore the…