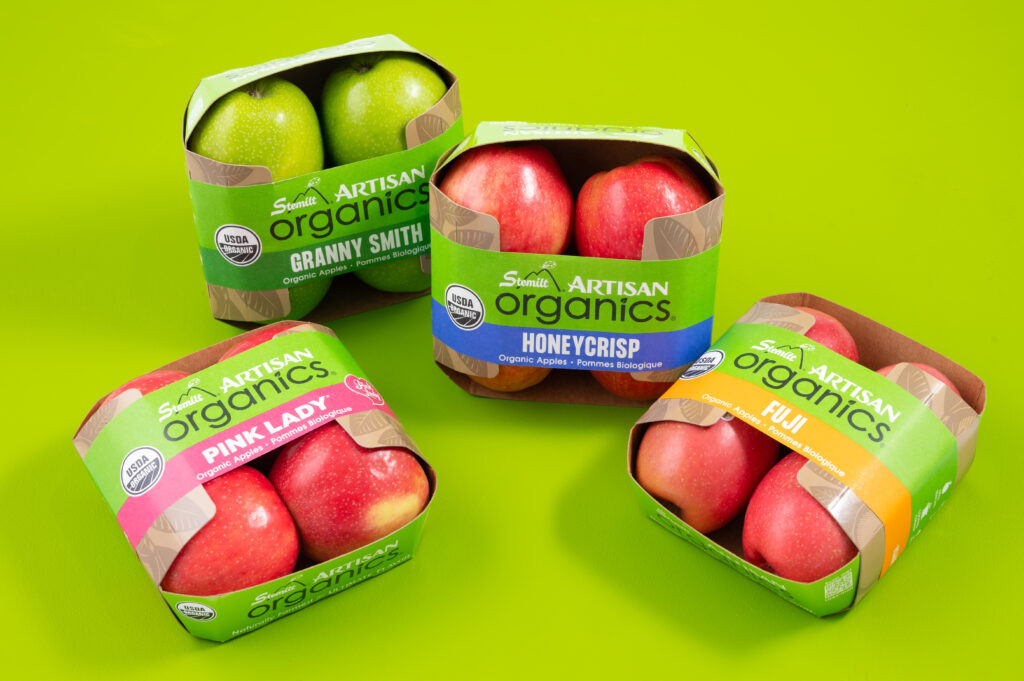
Simplify, Protect, and Present Your Products with Precision
Discover how our state-of-the-art banding solutions can improve packaging sustainability, enhance product presentation, and streamline your operation.
Reduce Product Damage & Overcome Over-Packaging
Did you know that product damage and over-packaging can eat up to 30% of your operational costs? Felins Banding machines offer a sleek, secure, and eco-friendly alternative—protecting both your products and your bottom line.
Additional benefits include
- Easy removal without tools
- Live, inline printing and band customization
- Vibrant, stunning graphics on pre-printed material
- Large selection of material & machine options
- Reduced packaging material usage
- Energy efficiency
- Eco-Friendly & Minimal Material Use
If you’re looking to reduce packaging waste without compromising security, banding machines are your answer. Instead of bulky boxes or large plastic wraps, a thin paper or plastic band can keep products securely bundled. This approach not only cuts down on shipping costs but also supports sustainable packaging goals.
- Enhanced Product Presentation
Banding offers a sleek, polished look that goes beyond merely “holding items together.” With options for custom-printed bands, you can showcase branding or important product details—like barcodes or promotional messaging—right on the band itself. Retailers appreciate how banding machines help them create an appealing display, especially for goods like club packs produce, and high-end consumer products.
- Cost & Labor Savings
Manual packaging operations or over-packaging can drain resources and inflate operational costs. Automating with a banding machine significantly reduces labor hours and material expenses by using only what’s necessary. You’ll avoid the hassle of dealing with adhesives, larger-than-needed boxes, or multiple layers of plastic wraps—factors that quickly drive up packaging budgets.
- Flexibility Across Industries
One of the greatest strengths of banding lies in its adaptability. From food to pharmaceutical, print materials, banking, or laundry, a robust banding solution can handle everything from delicate booklets and brochures to heavier items like disassembled furniture kits. The tension settings on our banding machines are adjustable, so you can securely wrap fragile goods without risking damage or distortion.
- User-Friendly & Low Maintenance
Our modern banding equipment is designed for quick setup, easy material changes, and minimal maintenance. Advanced features—like ultrasonic sealing technology, digital tension settings, and touch-screen, intuitive control panels—simplify operator training and minimize maintenance requirements. In many cases, banding lines integrate seamlessly into existing production processes. By choosing Felins, you also benefit from lifetime, dedicated technical support and service plans to keep downtime at bay.
Redefine Banding Precision with Ultrasonic Technology
If you’re looking for a top-tier banding solution that delivers efficiency, versatility, and eco-conscious performance, our ultrasonic banding machines rise to the challenge. Powered by high-performance cold-weld ultrasonic technology and guided by an intuitive touchscreen operator interface, these ATS machines offer countless customizable features—making them ideal for virtually any application. Beyond their engineering excellence, our ultrasonic banders also support the highest quality paper and plastic banding materials, giving you the flexibility to choose a sustainable paper band or a visually striking label that elevates your brand. Both our paper and plastic bands are recyclable and we have options that include post consumer recycled content.
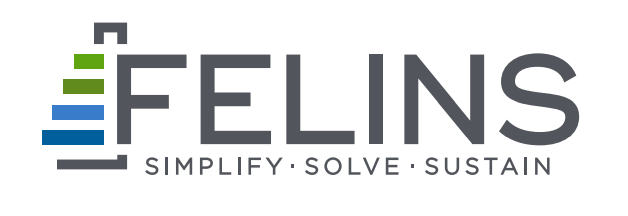
Banding Machine
- Heavy-Duty
- Lower energy consumption
- Countless customizable features
- Sustainable material compatibility
Looking for a heavy-duty banding solution that combines speed, consistency, and energy efficiency? Our top-of-the-line ultrasonic banding machine uses a fast, clean, and reliable cold-weld process—eliminating the variability common to heat seal systems. Plus, with lower energy consumption and sustainable material compatibility, it’s the perfect fit for businesses aiming to reduce waste without sacrificing performance.
Countless customizable features make this versatile bander ideal for virtually any product or application. Need extra capacity for larger items? Check out our Large Arch Banding System. And if you’re not in the market for a new unit, we also offer a fleet of gently used ATS US-2000 machines, each backed by the same factory warranty as our new models—so you get unwavering quality and peace of mind every step of the way.
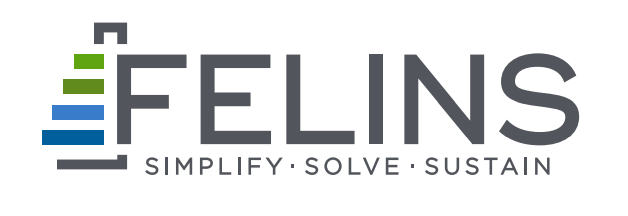
Banding Machine
- Bands up to 4″ wide
- Heavy-Duty
- Lower energy consumption
- Countless customizable features
- Sustainable material compatibility
This machine offers the same benefits as the US-2000, but can accommodate bands up to 4″ wide, giving you optimal space for branding and labeling. Additionally, this machine comes in stainless steel models, making it perfect for the food industry.
- Newest US-series model
- Heavy-Duty
- Lower energy consumption
- Countless customizable features
- Sustainable material compatibility
View Our Full Line of Ultrasonic Banding Machines
Learn about our inline automation, designed around ultrasonic banding machines!
Inline Automation & Advanced Features
Designed around our ultrasonic banding machines, we provide automated solutions in nearly every industry. These systems can be easily integrated into almost any production line, and they are capable of significantly decreasing labor costs while increasing throughput. They require little-to-no operator assistance and can be fully customized to meet your packaging needs. Below are just a few examples of automated solutions that we provide. If you don’t see what you need, contact us…chances are we’ve tried it before.
We have machines designed for multipacking, club-packing and more! Our automated counting and stacking machines are sure to boost efficiency while decreasing labor costs. These machines gently band products to ensure that they are not damaged and offer the ability to customize the label for date codes, ingredient lists, etc. during the banding process.
Designed around our ultrasonic banding machines, our feeding, stacking and banding (FSB) machines will efficiently and reliably count, stack, and sort your printed products. We provide a variety of different options and features to ensure that your automatic feeding and stacking machine works well for you.
Branding your products is quick and easy with automatic labeling systems. Designed to automatically label and sleeve your products, these machines are equipped with technology to perfectly position the pre-printed material on each bundle. The material is applied with the right amount of tension to ensure that the products are held together securely without being damaged. By adding an inline printer, these sleeving systems can also print variable data live on each band.
Inline Automation & Advanced Features Machines
Heat Seal Banding Machines
Perfect for growing facilities, our line of heat seal machines provides an excellent introduction to banding. Easy to operate and maintain, these machines will quickly improve your packaging operations with minimal investment in capital and operator training.
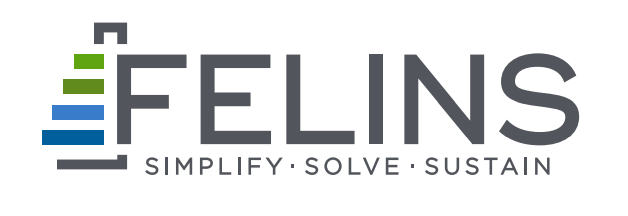
Banding Machine
- Easy-to-use and set-up
- Instantaneous, impulse heat seal
- Do not require any warmup time
- Cost effective
- Highly versatile
The ATS-MS series portable banding machines are the most elite heat seal banding machines on the market. These easy-to-use industrial heat seal banding machines create an instantaneous, impulse heat seal and do not require any warmup time, virtually eliminating the opportunity for burn-related injuries to operators and maintenance technicians. These machines are cost effective, easy to use and set-up, and are highly versatile for nearly limitless applications and products. Plus, they don’t require any compressed air!
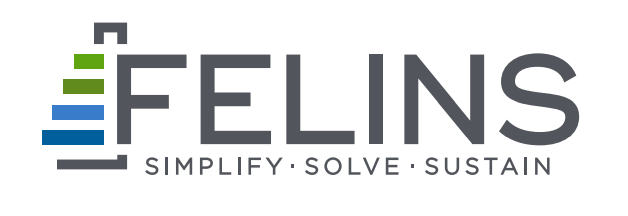
Banding Machine
- Easy-to-use and set-up
- Compact table-top design
- Highly versatile
View Felins’ Full Range of Heat Seal Banding Machines
By selecting the right banding machine—paper or plastic, manual or inline automation—you’re investing in a cleaner, more sustainable, and more efficient packaging process. Whether you need gentle handling for printed products or a high-speed solution to bundle heavy items, Felins’ portfolio of banding equipment is engineered to meet a broad range of industry requirements, from food to pharma, print to manufacturing. Embrace the modern face of packaging and see immediate improvements in both operational costs and brand presentation.
How We’ve Helped Companies Like Yours
Nothing speaks louder than real-world results. Here are just a few examples of how Felins’ banding machines have helped businesses across various industries streamline operations, cut costs, and enhance product presentation:
Ready to Transform
Your Packaging?
After seeing how Felins’ banding machines can revolutionize your packaging process—reducing labor, increasing throughput, and shrinking your environmental footprint—why wait? Here’s how to get started with us today.
Request a
Consultation
Our experts can help identify the right banding solution for your specific needs—no obligation, just insights.
Ask About
a Demo
Want to see the difference in real time? Schedule a live or virtual demo and experience the efficiency boost firsthand.
Ready for Smarter
Banding Solutions? Let’s Talk.
Fill out the form below, and our team will be in touch within 1 business day.
Popular Banding Machines FAQs
What Is Paper Banding?
Paper banding uses a narrow paper strap—often recyclable or compostable—to bundle items without excess plastic. Perfect for businesses prioritizing eco-friendly packaging, paper bands provide a secure hold and can be easily branded.
What is a Paper Banding Machine?
A banding machine wraps the paper banding material (also known as adhesive-free labels or automatic paper sleeves) around each product or bundle of products, then cuts and seals the band to itself automatically. The resulting packaging is easy to remove without tools, and allows for integration of creative graphics, branding and decoration. Paper banding offers a sustainable solution for businesses looking for recyclable labels or pulpable packaging around their product. Our banding machines are capable of running both paper banding and plastic banding so that you can have the flexibility you need for your projects. See our banding machine models below.
What is Plastic Banding?
Plastic banding has most of the same benefits and applications as paper banding, with some differences. Plastic banding is a common solution for companies in the Food, Healthcare, Manufacturing, E-commerce, and Pharmaceutical industries where a higher strenth band is required to prevent tearing or breaking.
What is a Plastic Banding Machine?
A plastic banding machine wraps the banding material, either plastic film or ribbon material, around each product or bundle of products then cuts and seals the band automatically to itself. Plastic banding is great for products that could be stored in a moist environment such as a refrigerator or freezer, projects that require a premium label for vibrant graphics, brand marketing, or informational details such as nutrition information or company information. Our banding machines are capable of running both paper banding and plastic banding so that you can have the flexibility you need for your projects. See our banding machine models below.
Guide: Understanding Banding Machine Types and Their Applications
Understanding Banding Machine Types and Their Applications
When exploring industrial packaging solutions, understanding the diverse world of banding machines becomes essential for optimizing your operation. From automatic banding machines to manual options, today’s market offers specialized solutions for every packaging need.
At Felins, sustainable packaging is our passion. No matter your application needs, we have systems — from table-top to fully-automatic paper and plastic banding machines to help you get the sustainable packaging solutions your company needs. We’ve put together this comprehensive guide on banding machines as a go-to resource to your pressing packaging questions.
For more information on how we can help you, contact our expert team and start saving on your packaging and labor costs.
Automatic Banding Systems: The Future of Efficiency
Modern automatic banding machines represent the pinnacle of packaging automation. These sophisticated systems can process thousands of units per hour, making them ideal for high-volume operations. While both banding and strapping machines can integrate seamlessly with existing production lines, banding provides more delicate tension control for unitizing products without damage. In contrast, strapping is best suited for higher-tension applications requiring high tensile strength straps.
For businesses handling products from printed products to cartons with healthcare products to food products, automatic banding machines provide near unmatched efficiency, and are an excellent choice for companies spanning a wide range of industries.
Paper Banding: The Sustainable Choice
Paper banding machines have gained significant traction as environmental concerns grow. These systems can use recyclable paper bands instead of plastic, making them perfect for print shops, currency handling, and sustainable packaging operations.
Table top paper banding units offer compact solutions for smaller operations, while industrial-scale models can handle large-volume applications.
The benefits? The paper banding process not only bundles products together but also presents them in an environmentally conscious way.
Material Compatibility and Options
Modern banding machines accommodate various materials beyond traditional options. While plastic banding remains popular for its versatility, there are a variety of different materials such as transparent film, paper banding, 100% TruePaper material, compostable materials, and recyclable plastic banding . The choice between heat seal, ultrasonic, or mechanical securing methods depends on your specific needs and material preferences.
By understanding these various banding machine types and their applications, businesses can make informed decisions about their packaging automation needs. Whether opting for a table-top paper banding solution or a full-scale automatic banding system, the right choice depends on your specific operational requirements, volume needs, and material preferences.
Selecting and Implementing Your Banding Solution (8 Things You Need to Know)
Understanding how to select, purchase, and implement a banding machine requires careful consideration of multiple factors. Let’s explore the key aspects of acquiring and operating these essential packaging tools, from initial purchase through ongoing maintenance.
#1 Evaluating Purchase Options and Suppliers
The banding machine market offers diverse options from leading suppliers — like the team here at Felins. When considering a purchase, it can be helpful to evaluate both new and used equipment options. Major suppliers may provide comprehensive catalogs, while specialized distributors offer expertise in specific industries. For operations seeking flexibility, rental and lease options provide an excellent way to test different models before committing to a purchase.
#2 Understanding Cost Considerations
Pricing varies significantly based on machine capabilities and specifications. While tabletop models offer cost-effective solutions for smaller operations, automated systems like the US-2000 TRW-FD-J represent larger investments with corresponding productivity benefits. Consider not just the initial price but also operating costs, including maintenance, repair, and consumables. Many suppliers offer financing options, making advanced banding technology accessible to operations of all sizes.
#3 Installation and Operator Training
Successful implementation begins with proper installation and comprehensive operator training. Whether you’re working with a small electric banding tool or a fully automated system, proper setup ensures optimal performance. Many manufacturers provide detailed instructions and training videos for their equipment. Professional installation services, particularly for larger systems, can prevent costly operational issues and ensure safety compliance.
#4 Maintenance and Repair Considerations
Regular maintenance extends equipment life and maintains operational efficiency. From simple tabletop models to sophisticated automated systems, establishing a preventive maintenance schedule is crucial. Common maintenance tasks include:
- Cleaning cutting mechanisms
- Checking air systems in pneumatic models
- Regular cleaning of equipment
- Lubricating wear surfaces
When repairs are needed, working with authorized service providers ensures access to genuine parts and expert technical support.
#5 Material Selection and Compatibility
Choosing the right banding materials significantly impacts performance. Whether processing banknotes, envelopes, or wood products, material selection must match both machine capabilities and product requirements. Modern systems can handle various materials, from traditional banding to specialized films. Consider factors like tension requirements, environmental conditions, and recycling capabilities when selecting materials.
#6 Integration with Existing Systems
Modern banding solutions often integrate with broader packaging operations. From simple semi-automatic units to fully automated systems, consideration must be given to workflow integration. This might include compatibility with existing conveyor systems, synchronization with other packaging equipment, or integration with production monitoring systems.
#7 Support and Resources
Access to ongoing support and resources ensures long-term success. Felins maintains trained experts, extensive technical documentation, parts inventories, and service networks.
Online resources often include operator guides, troubleshooting tips, and maintenance schedules.
Building a relationship with reliable suppliers ensures access to necessary support, from routine maintenance to emergency repairs.
#8 Future-Proofing Your Investment
Always think about the future — not just the here and now. When selecting a banding solution, consider future needs and growth potential. Many operations start with smaller semi-automatic models before transitioning to fully automated systems. Understanding upgrade paths and scalability options helps ensure your investment continues to meet evolving business needs. Consider factors such as:
- Production volume increases
- New product lines
- Changing material requirements in your planning process.
By carefully considering these aspects, organizations can make informed decisions about their banding equipment investments and ensure successful long-term implementation. Whether selecting a simple tabletop unit or a comprehensive automated system, thorough evaluation and planning facilitate optimal outcomes.
Industry Applications and Solutions: From Desktop to Industrial Scale
Understanding the diverse applications of banding technology reveals its crucial role across various industries. From desktop solutions in office environments to vertical systems in manufacturing, modern banding equipment addresses numerous packaging challenges.
Document and Mail Processing
The evolution of envelope and document handling has made significant strides through automated banding solutions. Modern systems efficiently process:
- High-volume bundling for documents, envelopes, printed cards, tickets and more with precise tension control and automated stacking and counting
- Multi-size envelope stacks, maintaining integrity while ensuring quick access
- Desktop publishing materials with clean, professional presentation
E-commerce and Retail Solutions
The growth of online retail has driven innovation in banding technology. From Amazon fulfillment centers to local depot operations, these systems provide:
- Rapid processing of variable-size packages
- Sheet bundling for efficient storage
- Custom kit assembly solutions
- Home delivery packaging optimization
Specialized Industry Solutions
Certain sectors require unique banding approaches and specialized solutions for:
- Pharmaceutical product bundling with tamper-evident features
- NSN (National Stock Number) compliant military packaging
- Temperature-sensitive material handling
- Clean room compatible systems for sterile environments
Integration and Workflow Enhancement
Modern banding systems serve as crucial components in larger automation strategies. Key considerations include:
- Vertical integration with existing production lines
- Material flow optimization through strategic placement
- Custom configurations for specific product requirements
- Smart system monitoring and maintenance alerts
The versatility of current banding technology enables businesses to streamline operations while maintaining product integrity. Whether implementing a simple desktop solution or a comprehensive industrial system, understanding these applications helps organizations maximize their investment in banding machine technology.
Here at Felins, we serve a variety of industries, including:
- Banking
- Consumer Goods
- Corrugated
- E-Commerce
- Floral
- Food
- Healthcare
- Laundry
- Mailing
- Manufacturing
- Pharmaceutical
- Textile
- Wood
Looking Forward: Emerging Applications
As technology evolves, new applications continue to emerge. Future developments focus on:
- Enhanced automation capabilities for varied product types
- Improved material handling for sustainable packaging options
- Advanced tracking and monitoring systems
- Integration with Industry 4.0 initiatives
This comprehensive understanding of applications across industries helps organizations identify the most effective banding solutions for their specific needs, ensuring optimal performance and return on investment.
Sustainability in Modern Banding Technology: Leading Environmental Innovation
The Environmental Challenge in Packaging
The scale of packaging waste presents a significant environmental challenge. According to EPA data, the United States generates over 82.2 million tons of municipal solid waste annually, representing 28% of total waste production. More concerning still, over one-third of this packaging waste ends up in landfills. This reality demands innovative solutions that can dramatically reduce packaging waste while maintaining product protection and presentation standards.
The Revolution in Packaging Mass Reduction
Modern banding technology represents a transformative approach to waste reduction. Through innovative design and material science, today’s banding solutions achieve up to 95% reduction in packaging mass compared to traditional methods. This dramatic decrease comes from a fundamental rethinking of how products are secured and bundled.
To understand the magnitude of this reduction, consider a visual comparison: while traditional packaging methods might fill an entire storage room with boxes and void fill materials, the equivalent amount of banding material might occupy just a small bin. This reduction in physical volume translates directly to reduced storage requirements, lower transportation costs, and significantly decreased environmental impact.
Circular Economy Integration
The commitment to sustainability extends beyond just reducing material usage. Modern banding solutions support a circular economy through several innovative approaches:
#1 Material Innovation
Advanced materials science has enabled the development of environmentally conscious options that maintain performance while reducing environmental impact. These include compostable plastic films engineered to break down naturally over time, and paper banding materials that seamlessly integrate with existing municipal recycling programs.
#2 Certified Materials
Particularly noteworthy is the use of FSC® (Forest Stewardship Council®) certified materials. These materials can be traced back to their source forests, ensuring responsible forest management practices throughout the supply chain. Additionally, innovative film technologies incorporating air bubbles significantly reduce resin requirements while maintaining structural integrity.
Equipment Sustainability
The environmental commitment extends to the equipment itself. Rather than following the traditional model of replacing older equipment, modern manufacturers employ several sustainable practices:
#1 Machine Rebuilding Programs
Instead of discarding aging equipment, comprehensive rebuilding programs extend machine life through electronics upgrades and mechanical refurbishment. This approach not only reduces waste but also makes advanced technology accessible to more businesses.
#2 Flexible Usage Models
Recognizing that packaging needs can be seasonal or project-specific, rental programs allow businesses to access needed equipment without the waste associated with unused machinery. This approach optimizes resource utilization across the industry.
#3 Energy Efficiency Innovation
Perhaps most impressive is the advancement in energy efficiency. Ultrasonic banding technology demonstrates remarkable efficiency, reducing electrical consumption significantly compared to traditional shrink film machines. This dramatic reduction in energy usage represents a significant step forward in sustainable packaging operations.
Comprehensive Organizational Commitment
True sustainability requires a holistic approach that extends beyond product offerings. Leading companies in the banding industry, like Felins, demonstrate this through internal initiatives:
- Paperless Operations: Since 2015, progressive policies have eliminated over tens of thousands of pounds of paper waste through digital transformation.
- Elimination of Single-Use Products: Comprehensive programs eliminate foam-based products and single-use containers, replacing them with sustainable alternatives.
- Resource Conservation: Installation of in-line water filtration systems and energy-efficient controls demonstrates commitment to resource conservation at every operational level.
Measurable Impact and Future Direction
The adoption of sustainable banding technology creates measurable environmental benefits:
- Material Reduction
- Energy Savings
- Waste Elimination
- Transportation Efficiency
Looking Forward
The future of sustainable packaging continues to evolve through ongoing innovation in:
- New biodegradable material development
- Enhanced energy efficiency technologies
- Improved material recovery systems
- Advanced waste reduction strategies
By embracing these sustainable technologies and practices, businesses can significantly reduce their environmental impact while maintaining or improving operational efficiency. This commitment to sustainability represents not just an environmental imperative but a competitive advantage in an increasingly environmentally conscious marketplace.
Operational Excellence and Industry Solutions: Mastering Banding Technology
Understanding how to operate and optimize banding equipment across diverse applications ensures maximum efficiency and return on investment. Let’s explore key operational aspects and industry-specific solutions that drive success in various sectors.
Food Industry Implementation
Food packaging demands unique considerations for safety and efficiency. Advanced banding solutions accommodate sensitive products like:
- Banana and fresh produce bundling with gentle tension control
- Napkin and food service supply organization
- Bundle creation for retail-ready presentation
- Sanitary design requirements for food-grade environments
- Single and club packs of sausage
- Unique skin pack trays that don’t work well with traditional pressure sensitive labels
Specialized Industry Solutions
Certain applications require unique approaches to banding. From antique book preservation to modern cardboard handling, specialized solutions address:
- Delicate material handling without surface damage
- Money bundling with security features
- Bird and animal feed packaging compliance
- Harbor and marine environment durability
Trade Show and Exhibition Insights
Industry events often showcase the latest innovations in banding technology. These venues typically highlight:
- New model introductions from leading manufacturers
- Hands-on demonstrations of handheld units
- Innovative applications across industries
- Networking with suppliers and industry experts
Support and Service Excellence
Maintaining optimal performance requires comprehensive support. Essential elements include:
- Video training resources for operator certification
- Near-immediate access to technical assistance
- Regular maintenance scheduling
- Quick resolution when equipment gets caught or jammed
Future Trends and Innovations
The banding industry continues to evolve, with developments focused on:
- Enhanced electronic controls for precision operation
- Advanced material handling capabilities
- Improved ergonomic design for operator comfort
- Integrated quality control systems
Understanding these operational aspects and industry applications helps organizations maximize their banding technology investment while ensuring consistent, high-quality results. Whether implementing a simple manual system or a complex automated solution, proper operation and maintenance remain crucial for long-term success.
The Evolution and Impact of Banding Technology in Modern Industry
The landscape of industrial packaging and bundling has undergone a remarkable transformation with the advent of modern banding technology. As businesses face increasing pressure to optimize efficiency while reducing costs and environmental impact, banding machines have emerged as a crucial solution across diverse sectors.
Understanding the Market Evolution
Today’s banding technology represents decades of innovation in industrial packaging. From simple manual strapping tools to sophisticated automated systems, the industry has consistently evolved to meet changing market demands. This progression has led to the development of diverse solutions, from compact desktop units handling banknotes and documents to industrial-scale systems managing heavy-duty materials.
The Shift Toward Automation
The transition from manual to automatic banding has revolutionized operational efficiency. Modern automatic banding machines now handle tasks that once required significant manual labor, processing thousands of units per hour with consistent precision. This automation revolution has particularly impacted industries dealing with high-volume packaging needs, from publishing houses to manufacturing facilities.
Environmental Considerations and Sustainability
As environmental consciousness grows, the banding industry has responded with innovative solutions. The introduction of paper banding machines and recyclable materials has provided sustainable alternatives to traditional plastic strapping. These developments align with global initiatives to reduce packaging waste while maintaining operational efficiency.
Economic Impact and Market Growth
The global banding machine market continues to expand, driven by:
- Increasing adoption across diverse industries
- Growing demand for automated packaging solutions
- Rising focus on operational efficiency
- Expanding e-commerce sector requirements
Industry Integration and Digital Transformation
Modern banding systems now integrate seamlessly with Industry 4.0 principles, incorporating:
- Advanced electronic controls for precise operation
- Digital monitoring capabilities
- Smart maintenance systems
- Automated quality control features
Meeting Contemporary Challenges
Today’s businesses face complex packaging challenges, including:
- Varying product sizes and materials
- High-speed production requirements
- Quality consistency demands
- Cost optimization needs
- Environmental compliance
The Role of Innovation
Continuous technological advancement has introduced features like:
- Tension control systems preventing material damage
- Quick-change mechanisms for different materials
- Enhanced safety features
- Improved energy efficiency
Market Response and Adaptation
The industry has responded to evolving needs with:
- Specialized solutions for specific sectors
- Flexible rental and leasing options
- Comprehensive support services
- Advanced training programs
As we delve deeper into the world of banding technology, understanding these foundational elements becomes crucial for businesses seeking to optimize their operations. Whether managing small-scale bundling needs or implementing large-scale automated solutions, the right banding technology can significantly impact operational success.
As we continue to explore every aspect of banding technology — from basic principles to advanced applications — our goal here at Felins is to help you make informed decisions about implementing these crucial systems in your operations. Through detailed analysis and practical insights, we’ll examine how modern banding solutions can transform your packaging processes while delivering substantial returns on investment.
Business Benefits and ROI: Understanding the Value Proposition of Banding Technology
When evaluating banding solutions, from simple strapping tools to sophisticated automated systems, understanding the comprehensive return on investment helps organizations make informed decisions. Let’s explore the multifaceted benefits and economic advantages of implementing modern banding technology.
Cost Reduction Through Operational Efficiency
Modern banding systems deliver significant operational savings. Organizations implementing these solutions typically experience substantial reductions in packaging material costs through precise tensioning and minimal waste.
For example, when packaging vegetables, asparagus, or other produce, automated systems ensure consistent material usage without over-strapping.
Labor cost optimization represents another crucial benefit. A single operator using an automated system can accomplish what previously required multiple staff members, particularly in high-volume operations handling aluminum tubes, as an example. This efficiency extends across industries, from manufacturing facilities to distribution centers.
Quality Improvements and Waste Reduction
Investment in quality banding equipment from respected suppliers yields measurable improvements:
- Consistent tensioning prevents product damage and reduces returns
- Automated systems eliminate human error in strap placement
- Proper sealing mechanisms, whether using crimpers or heat sealers, ensure secure bundling
- Advanced features prevent common issues like cracking or splitting
Sustainability and Environmental Benefits
Modern banding solutions contribute to environmental initiatives through:
- Reduced material consumption compared to traditional packaging methods
- Options for recyclable strapping materials
- Decreased waste from damaged products
- Lower energy consumption with efficient controls systems
Space Utilization and Workflow Enhancement
Implementing banding technology optimizes facility space through:
- Compact equipment footprints, even for automated systems
- Improved product organization and storage
- Efficient cart and material handling integration
- Strategic placement options for workflow optimization
Long-term Cost Analysis
When calculating ROI, consider:
Initial Equipment Investment
- Purchase price comparison across manufacturers
- Installation and training costs
Operational Costs
- Material costs per unit
- Labor requirements
- Maintenance and service needs
- Energy consumption
Productivity Gains
- Increased units processed per hour
- Reduced downtime
- Improved accuracy rates
- Enhanced worker safety
The True Value Proposition
Beyond direct cost savings, modern banding systems deliver:
- Improved customer satisfaction through consistent packaging
- Enhanced brand reputation with professional presentation
- Reduced workplace injuries from manual strapping
- Increased operational flexibility
By understanding these comprehensive benefits, organizations can better evaluate the true ROI of banding technology implementation. Whether selecting a basic strapping tool or investing in a sophisticated automated system, the key lies in matching the solution to specific operational needs while considering both immediate and long-term benefits.
This investment analysis should consider not just the immediate cost savings but also the broader operational improvements and growth potential that modern banding technology enables. From small operations to large facilities managing complex packaging requirements, the right banding solution can deliver substantial returns while positioning organizations for future success.
Banding vs. Alternative Packaging Methods: A Comprehensive Analysis
When evaluating packaging solutions for your operation, understanding the full spectrum of options helps make an informed decision. Let’s explore how modern banding technology compares to traditional packaging methods across various applications and industries.
Cost Analysis: Understanding the Bottom Line
Initial Investment Considerations
The upfront costs of packaging equipment vary significantly across solutions. Commercial banding systems represent a more substantial capital expenditure. However, when evaluating these costs, it’s crucial to consider the long-term savings in both materials and labor.
For example, in vegetable and fruits packaging operations, traditional methods often require multiple materials – from plastic crates to labels and adhesives. In contrast, modern inline banding systems can secure produce like broccoli and other veggies with a single band, significantly reducing material costs.
Environmental Impact Assessment
Material Reduction
Modern banding solutions significantly reduce packaging waste compared to traditional methods. Consider these applications:
Retail Packaging:
- Traditional methods might require boxes, vinyl wrapping, and additional protective materials
Laboratory and Specialized Settings:
In laboratory environments where precision is paramount, modern banding systems offer unique advantages:
- Minimal particle generation compared to traditional packaging methods
Shipping and Logistics:
In parcel and shipping operations:
- Conventional methods typically involve multiple steps and materials
- Modern banding provides:
- Speedy processing
- Easy-to-remove bands
Specialized Industry Solutions:
- Modern banding systems excel at:
- Precise tension for delicate items
- Clean operation for food safety
- Temperature-controlled environments
Manufacturing and Assembly:
- Conventional packaging often requires:
- Multiple material types
- Complex sealing processes
- Extensive labor
- Banding solutions offer:
- Streamlined processes
- Consistent tension
- Reduced material waste
Cost-Benefit Analysis
Return on Investment
When evaluating packaging solutions, consider:
- Equipment rentals vs. purchase options
- Job-specific requirements
- Material costs over time
- Labor savings potential
A mini banding system might pay for itself within months through reduced material usage alone, while larger commercial systems often demonstrate ROI through increased efficiency and reduced labor costs.
Future Considerations
The packaging industry continues to evolve with:
- New materials for specific applications
- Advanced automation features
- Improved environmental sustainability
- Enhanced safety features
Whether you’re handling delicate laboratory samples or heavy industrial loads, understanding these comparisons helps inform your packaging decisions.
The Digital Evolution Meets Banding Machines
The landscape of industrial banding has undergone a remarkable transformation, moving from simple mechanical systems to sophisticated digital solutions. Understanding these technological advances helps operations managers make informed decisions about upgrading their packaging systems.
Smart Manufacturing Integration
Modern banding machines can now incorporate sophisticated digital controls that would seem like science fiction only a few decades ago. These systems feature:
Data Management and Analytics
Real-Time Monitoring Capabilities
Today’s systems can register and track multiple parameters simultaneously:
- Band tension variations
- Production rates
- Material usage patterns
- System performance metrics
This data collection goes far beyond simple copy-and-paste reporting. Modern machines create comprehensive performance logs that help operations managers optimize their packaging lines, creating a digital battlefront against inefficiency.
Safety and Automation Features
Enhanced Safety Protocols
Modern systems incorporate multiple safety features to protect operators from potential hazards:
- Emergency stop systems
- Protective cabinet enclosures
These safety features work in concert with productivity enhancements, ensuring that while max output is achieved, worker protection remains paramount.
Smart Labeling Integration
Advanced Identification Systems
Modern machines now incorporate sophisticated labeling capabilities:
- Real-time print-and-apply systems
- Automated set numbering
This integration eliminates the need for separate labeling stations, streamlining the entire packaging process.
Maintenance Innovation
Predictive Maintenance Systems
Modern banding equipment employs sophisticated monitoring systems that can:
- Predict component wear
- Schedule preventive maintenance
- Alert operators to potential issues
This proactive approach helps prevent unexpected downtime and extends equipment life, particularly important for operations running multiple jobs simultaneously.
Energy Efficiency Advances
Power Management Systems
Contemporary machines incorporate advanced energy-saving features:
- Smart standby modes
- Energy usage monitoring
These innovations significantly reduce operational costs while maintaining peak performance.
User Interface Improvements
Operator-Friendly Controls
Modern interfaces now feature:
- Touch-screen controls
- Automated settings management
- Easy-to-navigate menus
Gone are the days of complex manual adjustments; today’s systems offer intuitive controls that even new operators can master quickly.
Future Developments
Emerging Technologies
The industry continues to evolve with:
- AI-driven optimization
- IoT connectivity
Cost Considerations
When evaluating these technological advances, consider:
- Initial cash investment
- Long-term savings
- Productivity gains
- Training requirements
Many manufacturers offer flexible payment options, and some even list certified pre-owned equipment, making advanced technology more accessible to smaller operations.
Integration Capabilities
Modern systems can seamlessly connect with:
- Existing ERP systems
- Automated tray loading systems
- Conveyor systems
This connectivity creates a comprehensive packaging solution that can adapt to changing production needs.
Safety Protocols and Best Practices in Banding Machine Operations — A Deeper Look
The safe operation of banding equipment requires a thorough understanding of both mechanical and operational safety principles. While modern banding machines incorporate numerous safety features, proper training and adherence to protocols remain essential for preventing workplace incidents and ensuring optimal operation.
Operator Safety Training Requirements
Every operator must complete a structured training program before working with banding equipment. This training should cover:
- Understanding Machine Components. Operators need detailed knowledge of key mechanical elements, including tensioning systems, pneumatic components, and emergency stops. This understanding extends to both standard operations and potential failure modes, ensuring operators can respond appropriately to any situation.
- Operational Safety Procedures. Safe operation involves more than simply knowing which buttons to press.
- Emergency Response Protocols. When incidents occur, immediate and appropriate response can prevent injury and minimize equipment damage. Operators must understand emergency procedures, including:
- Immediate machine shutdown procedures
- Clear communication protocols
- Incident documentation requirements
- First aid and emergency contact procedures
Personal Protective Equipment (PPE) Requirements
Proper PPE forms the first line of defense against workplace injuries. Required equipment typically includes:
Basic Protection
- Safety glasses with side shields
- Cut-resistant gloves for material handling
- Steel-toed safety shoes
- Appropriate work clothing that prevents entanglement
Specialized Protection
Certain applications, particularly those involving pneumatic systems or specialized labels, may require additional protective gear.
Machine Safety Features and Protocols
Contemporary banding equipment incorporates various safety features that operators must understand and maintain:
Physical Guards
- Belly guards protecting access to moving parts
- Emergency stop systems strategically placed for quick access
- Safety interlocks preventing operation when guards are removed
- Proper guarding around glue application systems, where applicable
Electronic Safety Systems
- Light curtains detecting operator presence in danger zones
- Automatic shutdown systems
- Emergency stop circuits
- Safety monitoring systems
Maintenance Safety Requirements
Regular maintenance must follow strict safety protocols:
Lockout/Tagout Procedures
- Proper power disconnection procedures
- Clear communication of maintenance status
- Verification of energy isolation
- Documentation of maintenance activities
Regular safety inspections should examine:
Critical Components
- Tension control systems
- Emergency stop functionality
- Guard integrity
- Safety interlock operation
Maintaining proper safety records is crucial for both compliance and continuous improvement:
Required Documentation
- Training completion records
- Inspection logs
- Incident reports
- Maintenance records
- Safety meeting notes
Industry-Specific Considerations
Different operating environments may require specific safety considerations.
Manufacturing Environments
- Integration with existing safety systems
- Coordination with material handling equipment
- Proper spacing and access requirements
Warehouse Operations
- Traffic management around equipment
- Material staging protocols
- Safe loading and unloading procedures
Emergency Response Planning
Every facility should maintain detailed emergency response plans, such as:
Response Protocols
- Clear evacuation routes
- Emergency contact information
- First aid procedures
- Incident reporting requirements
Future Safety Considerations
As technology advances, safety requirements continue to evolve. Organizations must stay current with:
Regulatory Updates
- New safety standards
- Updated compliance requirements
- Industry best practices
- Equipment-specific guidelines
Through proper attention to these safety protocols and best practices, organizations can maintain safe and efficient banding operations while protecting their most valuable asset – their employees. Regular review and updates of these procedures ensure continued safety and operational excellence.
Felins: Your Comprehensive Partner in Advanced Banding Technology
As a leader in sustainable packaging solutions, Felins stands at the forefront of banding technology innovation, offering comprehensive solutions that transform how businesses approach their packaging operations. With decades of experience and a commitment to sustainability, we provide cutting-edge banding machines and solutions that optimize efficiency while reducing environmental impact.
Comprehensive Solutions Portfolio
Felins offers a complete range of banding solutions:
- Ultrasonic banding machines featuring cold-weld technology
- Paper and plastic banding systems for various applications
- Heat seal machines for growing operations
- Automated inline solutions for high-volume production
- Custom solutions tailored to specific industry needs
Industry Expertise
Felins serves numerous sectors including:
- Banking and financial services
- Consumer goods and retail
- E-commerce and distribution
- Healthcare and pharmaceutical
- Manufacturing and industrial
- Food processing and packaging
- Printing and publishing
- Textile and laundry services
Commitment to Sustainability
At the heart of Felins’ operations is a dedication to environmental responsibility, demonstrated through:
- Paper banding solutions that reduce packaging waste by up to 95%
- Energy-efficient ultrasonic technology
- FSC®-certified materials options
- Machines designed for optimal material usage
- Solutions that support circular economy initiatives
Customer Support Excellence
We distinguish ourselves through comprehensive support services:
- Expert technical assistance
- Comprehensive operator training
- Preventive maintenance programs
- Emergency service response
- Detailed documentation and resources
- Online troubleshooting assistance
Innovation Leadership
We continue to push boundaries in banding technology through:
- Advanced automation capabilities
- Integration with Industry 4.0 initiatives
- Smart monitoring systems
- Energy-efficient design innovations
- Customizable solutions for unique applications
Getting Started with Felins
For businesses looking to optimize their packaging operations, Felins offers:
- Customized solution consulting
- Equipment demonstrations
- ROI analysis assistance
- Flexible purchase options
- Implementation support
- Ongoing technical assistance
Contact us at (800) 843-5667 or browse our website more to discover how our banding solutions can transform your packaging operations while reducing costs and environmental impact. With a commitment to sustainability, innovation, and customer success, Felins continues to set the standard for excellence in industrial banding technology.