With the introduction of automation, manual bundling is quickly becoming a thing of the past. Companies are replacing several stand-alone machines for one automated system that gets the job done better than ever before. If you aren’t sure if banding automation is the right solution for you, consider these seven signs of operations that could benefit from automation.
VOLUME.
Stand-alone, semi-automatic machines have much shorter lifespans than fully-automated systems. If used for at least one 8-hour shift each day, they can wear quickly and lead to unexpected pauses in production due to maintenance. These breaks significantly impact productivity, throughput, and ROI.
If you have more than two full-time machine operators, you’ll likely benefit from investing in an automated solution that will accommodate a higher volume of product than stand-alone or table-top machines.
COST.
Stand-alone machines are an excellent investment for companies with low volume who have minimal experience with bundling. However, once volume increases, stand-alone machines often experience more frequent breakages than automation. If you’re spending more money on spare parts than what you originally paid for your machine, it may be time to invest in automation.
Manual bundling can also quickly become costly if there is a workplace injury. In fact, in addition to “acute trauma such as cuts or fractures,” manual operations “may cause cumulative disorders due to gradual and cumulative deterioration of the musculoskeletal system through continuous lifting/handling activities.” If you’re concerned about, or have recently incurred, injury-related costs, consider a semi- or fully-automated solution. Most systems reduce, and sometimes eliminate, manual operation and handling.
PRINTING.
Automated banding machines can be equipped with variable data printers that use information from an uploaded database or file to print data on the band of each bundle. These printers make the process of printing on banding material more efficient and minimize the amount of leftover, unusable pre-printed material.
TIME.
Manual bundling is extraordinarily time consuming, even when mastered. Automated systems can run continuously with minimal downtime between bundles. Without the need for even the shortest of breaks, automation quickly increases productivity and throughput.
UNIFORMITY.
Some applications require every band to be placed in the exact same location on each bundle. With manual operation, consistency becomes difficult as there is a high potential for human error. But, with automation, you can be confident that each band will sit in the same spot of each bundle – every time.
BRANDING.
Bundling is considered end-line packaging but rarely is the final packaging step. Instead, bundles pass through one, if not two, additional lines to be labeled and prepped to be display-ready. But, with the introduction of variable data printers to banding automation systems, bundling and labeling can now occur in the same step. So, if you’re looking to band your products while maintaining your brand look and feel, automation should be on your radar.
VARYING PRODUCT & BUNDLE SIZES.
Some stand-alone machines are designed to accommodate a specific bundle size. Automated systems often feature sensors that determine bundle height and width before completing each band. This way, bundles of varying size can easily pass through the same system without manually updating settings.
If you’re suffering from any of the signs above, give us a call! We’d love to find a Felins solution for you.
MORE INSIGHT...
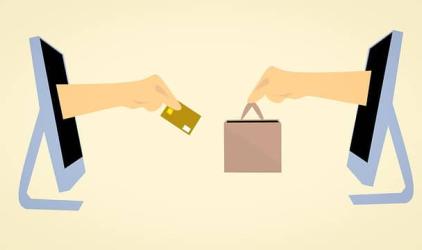
LOOK OUT FOR THESE E-COMMERCE PACKAGING TRENDS IN 2024
Discover the upcoming packaging and e-commerce trends in 2024. These changes are set to reshape the way products are packaged and delivered, focusing on sustainability, efficiency, and creative solutions. Let’s take a closer look at the…
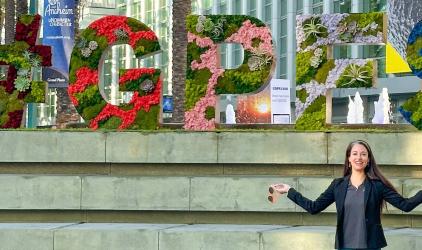
Global Produce and Floral Show 2023 – Trade Show Recap with Felins Packaging
The Felins team was thrilled to connect with fresh produce and floral packaging leaders at the vibrant Global Produce and Floral Show (GPFS) 2023 in Anaheim last week. As the premier trade show for the latest in produce and floral products as…
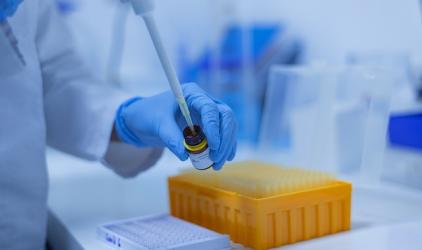
WHAT TO CONSIDER WHEN DECIDING ON PHARMACEUTICAL PACKAGING
Packaging regulations can be daunting, especially in the highly regulated world of pharmaceuticals. Ensuring that pharmaceutical products are packaged safely, securely, and in compliance with all applicable standards is not only a legal…